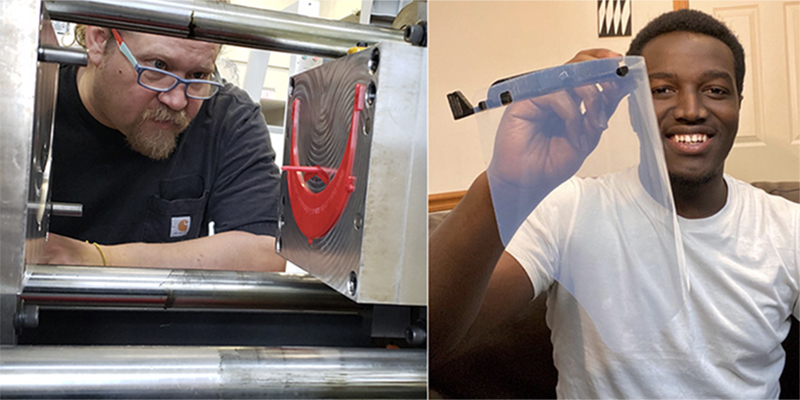
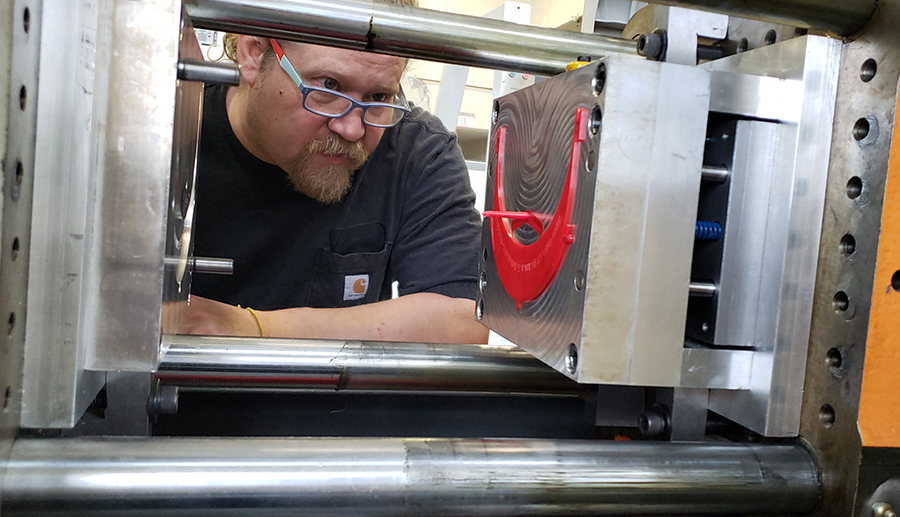
Miami making hundreds of face shields to help health care workers
College of Engineering and Computing, the Regionals and an engineering student are involved
By Margo Kissell, university news and communications
An injection-molded headband
Miami University’s department of mechanical and manufacturing engineering (MME) is making at least 500 face shields for health care workers using an injection molding process it developed.
Meanwhile, at the Regionals, the department of engineering technology (ENT) is utilizing 3D printing technology to make face shields.
After coordinating strategy-planning meetings with both MME and ENT, the team decided their capabilities and available materials could best serve the needs for personal protective equipment by making face shields, said Jim Oris, vice president for research and innovation.
"I am so proud to be part of this team of talented engineers who came forward with ways to manufacture a large number of face shields that can be used by first responders, health care workers, front line staff members or the general public,” Oris said.
Karl Reiff shows a completed face shield.
“We are now working out ways to get them into the hands of those individuals."
Amit Shukla, chair and professor of MME, said an initial prototype using 3D printing took nearly three hours to make one face shield. “We decided to speed up the process by looking at other technologies we have in our labs,” he said.
Last week, the department that is part of the College of Engineering and Computing started using an injection molding process, enabling it to produce 350 face shields.
It takes about 20 seconds to make a headband, which is then assembled to a three-hole punched acrylic shield.
Shukla said they would like to produce at least 500.
“We have been part of a UC Health team discussion, and they have a need for at least 5,000 of these face shields.” Other collaborators are involved, he noted.
“Our efforts will be more locally directed to help Oxford and Butler County,” he said.
Shukla credited MME technical staff Karl Reiff and Brad Martin as the primary personnel on the project using equipment housed in a Garland Hall lab.
“It’s great to be able to contribute something,” said Reiff (Miami ’94), who had worked in the automotive plastics industry for a decade before joining Miami in 2004. “Having the first one made was a wonderful feeling.”
Student 3D printing face shields at home
Regis Rugerinyange holds one of his 3D-printed face shields.
Regis Rugerinyange, a first-year student from Rwanda majoring in mechanical engineering, has printed 380 face shields in recent weeks using a 3D printer at the West Chester home where he is staying.
Unable to return to Rwanda this spring because of travel restrictions, Rugerinyange was motivated to do something positive.
“The main reason I wanted to do this was the need to take part in the global fight against the coronavirus,” he said. “It all starts with simple acts like washing your hands, practicing social distancing, staying at home, to helping our health care workers meet their rising demand for personal protective equipment like gloves, face masks and face shields.”
He has developed contacts with area medical facilities and fire departments, where he has distributed the gear.
“It is in moments like these people from any field of work need to put together their strengths or energy to support those in need,” he said. “I just believe that it is the only way to win this fight against the coronavirus.”
Regionals team shifts gears
The department of engineering technology at the Regionals houses an additive manufacturing (AM) laboratory equipped with various 3D printers, 3D scanners and post-processing tools. The AM lab equipment is spread across the Hamilton and Middletown campuses to provide easy access for the ENT majors to utilize the available equipment and resources for their course projects and lab assignments.
The lab is staffed and supervised by Frank Tonner, a senior technical specialist in ENT who normally spends his time managing the laboratories and training students on operating 3D printing equipment. When the COVID-19 pandemic spread, that work stopped, and Tonner and Mert Bal, associate professor and coordinator of electromechanical engineering technology, began producing face shields.
“For me, this was a great opportunity for the department of engineering and technology (ENT) to immediately respond to community needs based on our experience with 3D printers,” said Ayo Abatan, chair and professor of engineering and technology.
“I am proud of the involvement of my colleagues, Frank and Mert, in the production of sample PPEs for use by frontline workers in the battle against COVID-19.”